What is Porosity in Welding: Typical Resources and Reliable Remedies
Wiki Article
Porosity in Welding: Identifying Common Issues and Implementing Finest Practices for Prevention
Porosity in welding is a prevalent concern that usually goes undetected up until it causes substantial troubles with the stability of welds. In this conversation, we will certainly explore the vital aspects contributing to porosity formation, examine its harmful effects on weld efficiency, and go over the best techniques that can be embraced to minimize porosity event in welding processes.Usual Sources Of Porosity
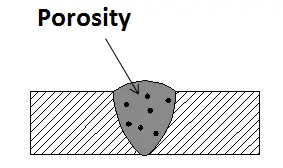
Utilizing unclean or damp filler products can present impurities into the weld, contributing to porosity issues. To alleviate these common causes of porosity, complete cleansing of base steels, correct securing gas selection, and adherence to optimal welding parameters are vital methods in accomplishing high-grade, porosity-free welds.
Influence of Porosity on Weld Top Quality

The presence of porosity in welding can substantially endanger the architectural stability and mechanical buildings of bonded joints. Porosity develops gaps within the weld steel, deteriorating its general stamina and load-bearing capability. These voids serve as tension concentration factors, making the weld much more vulnerable to breaking and failure under applied lots. In addition, porosity can minimize the weld's resistance to rust and other environmental variables, better lessening its durability and efficiency.
Welds with high porosity levels often tend to exhibit reduced impact stamina and reduced capability to flaw plastically before fracturing. Porosity can hamper the weld's capacity to efficiently send forces, leading to early weld failure and prospective safety dangers in vital frameworks.
Best Practices for Porosity Avoidance
To boost the structural stability and top quality of bonded joints, what particular procedures can be applied to reduce the incident of porosity throughout the welding procedure? Porosity prevention in welding is important to make certain the integrity and strength of the final weld. One efficient technique is proper cleaning of the check these guys out base metal, eliminating any kind of impurities such as rust, oil, paint, or moisture that could lead to gas entrapment. Guaranteeing that the welding devices remains in excellent problem, with tidy consumables and appropriate gas flow rates, can also considerably minimize porosity. In addition, keeping a secure arc and regulating the welding parameters, such as voltage, current, and travel speed, helps create a consistent weld pool that minimizes the risk of gas entrapment. Using the appropriate welding strategy for the particular material being welded, such as adjusting the welding angle and weapon setting, can even more avoid porosity. Routine evaluation of welds and immediate remediation of any kind of concerns identified throughout the welding procedure are necessary techniques to avoid porosity and generate high-grade welds.Significance of Correct Welding Methods
Executing correct welding methods is paramount in making certain the structural integrity and high quality of welded joints, constructing upon the foundation of effective porosity avoidance procedures. Welding techniques straight impact the overall toughness and sturdiness of the bonded structure. One vital element of correct welding methods is keeping the appropriate warm input. Excessive warmth can result in raised porosity because of the entrapment of gases in the weld swimming pool. Alternatively, inadequate warmth may lead to insufficient combination, page developing potential powerlessness in the joint. Additionally, utilizing the proper welding parameters, such as voltage, present, and take a trip speed, is vital for achieving sound welds with marginal porosity.In addition, the choice of welding process, whether it be MIG, TIG, or stick welding, must straighten with the details needs of the project to ensure optimal results. Appropriate cleaning and preparation of the base metal, in addition to choosing the ideal filler product, are likewise important parts of efficient welding methods. By adhering to these finest methods, welders can reduce the danger of porosity formation and produce top quality, structurally sound welds.

Testing and Quality Assurance Actions
Testing treatments are necessary to find and stop porosity in welding, making sure the stamina and resilience of the last item. Non-destructive testing methods such as ultrasonic screening, radiographic screening, and visual evaluation are commonly used to recognize prospective problems like porosity.Carrying out pre-weld and post-weld inspections is likewise crucial in keeping high quality control criteria. Pre-weld evaluations involve confirming the materials, devices settings, and sanitation of the work location to avoid contamination. Post-weld examinations, on the other hand, examine the final weld for any kind of issues, consisting of porosity, and validate that it fulfills specified criteria. Executing a thorough high quality control strategy that includes complete testing treatments and inspections is extremely important to minimizing porosity concerns and guaranteeing the overall high quality of bonded joints.
Conclusion
In verdict, porosity in news welding can be a typical issue that influences the quality of welds. By identifying the typical reasons for porosity and carrying out ideal practices for prevention, such as proper welding methods and testing procedures, welders can make certain top quality and reliable welds. It is necessary to focus on avoidance techniques to lessen the event of porosity and preserve the stability of welded structures.Report this wiki page